Achieving Sharp Vertical Shots on a Tripod
Achieving Sharp Vertical Shots on a Tripod - Selecting Stable Gear for Vertical Framing
For achieving sharp vertical photographs, the choice of your support equipment is crucial. The tripod body itself, encompassing its legs and central column, needs to provide exceptional stability to prevent camera shake and any detrimental vibration, particularly when supporting heavier cameras or lenses. Just as important is the head, often a ball head, which must allow for both smooth motion and exact fine-tuning required to frame vertical shots precisely. Maximizing stability frequently involves keeping the tripod relatively low, utilizing wider leg angles for a solid base rather than extending to its full height. Selecting gear built with this fundamental sturdiness ensures a dependable foundation, freeing you to focus entirely on creative composition.
Here are some points regarding the physical aspects of gear selection for stabilizing a camera for vertical image capture:
1. Mounting a camera vertically significantly elevates its center of mass relative to the tripod's apex and main column axis. This geometric shift inherently increases the torque and bending moments applied to the tripod structure by gravity and external forces (like wind or touch), making the entire system much more sensitive to resonant vibrations and flex than when the camera is mounted horizontally at the same height.
2. While convenient for many applications, the common ball head's locking mechanism relies on clamping pressure applied to a spherical surface. When heavily tilted 90 degrees to hold a camera vertically, the load distribution becomes highly asymmetrical, potentially leading to 'creep' – a gradual, slight shift or sag – or micro-movements within the joint under sustained load or minor vibration. This highlights a limitation in maintaining absolute positional rigidity compared to heads designed with separate axes of control.
3. Utilizing an L-bracket to attach the camera in vertical orientation directly repositions the camera's mounting point so its weight is centered directly above the tripod head's rotational axes and the tripod legs. This minimizes the cantilevered load that occurs when tilting a standard camera-and-plate setup 90 degrees using only the head, thereby significantly reducing the bending stresses on the head and plate interface that can introduce flex and instability.
4. The ability of tripod leg materials and joint designs to damp vibrations becomes exceptionally critical when supporting a camera elevated for vertical shots. Energy from external disturbances is amplified by the height and off-axis mass; materials like certain composites are less prone to sustained oscillation compared to some metals, meaning they absorb and dissipate vibrational energy more quickly, leading to faster settling and less risk of motion blur from lingering tremors.
5. The mechanical coupling between the camera body and the quick-release plate, and between the plate and the tripod head clamp, represents a potential point of weakness. Systems employing tight tolerances and robust metal-to-metal contact across substantial surface areas, as seen in high-quality dovetail-style interfaces, minimize minute rotational play or flex at this critical junction, a factor that becomes proportionally more significant and detrimental when the camera's weight is levered vertically.
Achieving Sharp Vertical Shots on a Tripod - Securing the Camera to Prevent Movement
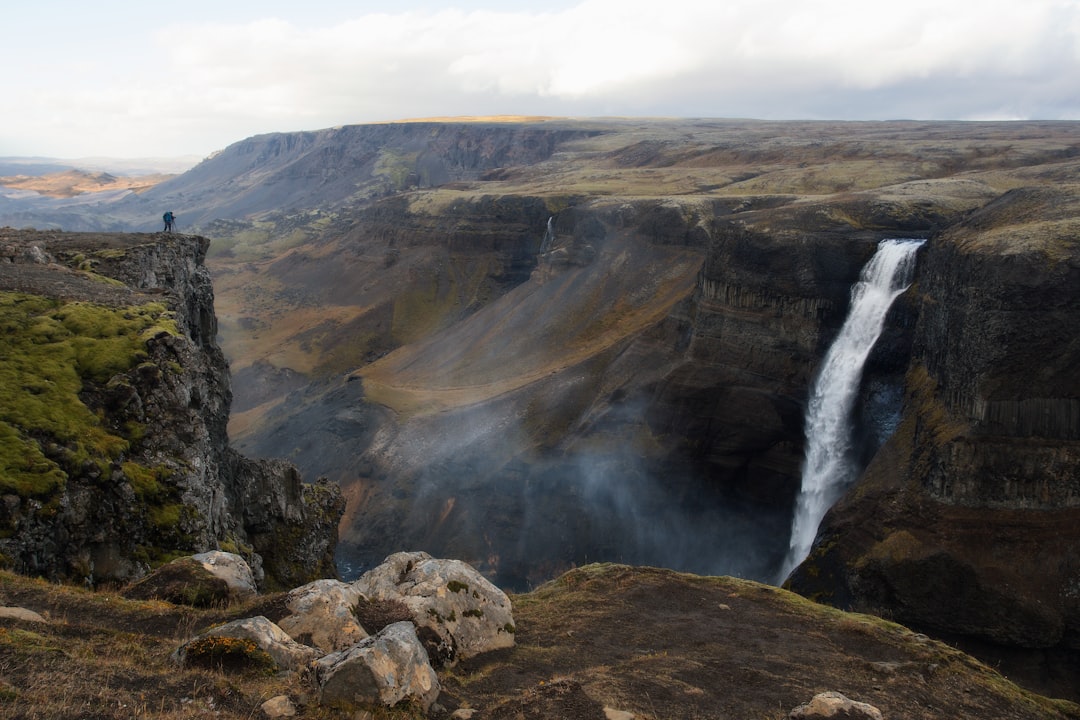
Ensuring your camera stays exactly put is fundamental once it's on the tripod, particularly for those tall vertical compositions. The link between the camera body and the tripod head – often via a quick-release plate system or a direct screw mount – has to be absolutely free of wobble or play. Cinch it down firmly; any looseness here is a guaranteed path to blur. Getting the tripod itself level is a necessary first step, but confirming your camera rig remains balanced once mounted vertically is also key; a small level can offer a quick check. Once set, treat the entire assembly with extreme caution. Even the slightest bump or adjustment can introduce vibrations or minuscule shifts that ruin sharpness. Patience and minimal interaction after framing are your allies.
It is perhaps counter-intuitive, but seemingly minor factors can significantly undermine the stability required for critically sharp vertical images, even when using substantial support systems:
The discrete mechanical action of a camera's internal shutter, often involving rapid mass movement and abrupt stops, imparts transient impulse forces onto the camera body. These impulses propagate through the camera and its mounting points into the support structure, potentially exciting vibrations that can last for milliseconds, particularly problematic during longer exposures where the sensor remains active.
Every camera-tripod assembly constitutes a unique, complex mechanical system with inherent natural frequencies at which it readily oscillates. Minute external disturbances, such as faint ground tremors, wind gusts, or even internal vibrations from the camera, if their frequencies align with these resonant points, can trigger disproportionately large amplitude vibrations that are visually imperceptible but sufficient to cause blur.
Attaching mass, typically via a hook beneath the center column, doesn't merely anchor the tripod; it fundamentally alters the system's total mass distribution and inertia. This shift changes the natural resonant frequencies, often moving them away from common disturbance frequencies, and critically, tends to increase the system's overall damping, meaning any induced vibrations decay faster, reducing the time window during which motion blur might occur.
Beyond the tripod and head components, subtle structural deformations can occur within the camera body itself or at the lens mount interface under the leverage exerted by the camera's weight when oriented vertically. This internal flexing, though measured in micrometers, represents a displacement of the sensor plane relative to the optical axis during the exposure, directly impacting image sharpness regardless of the tripod's external rigidity.
The tapered design of most tripod legs means that extending the lower, smaller-diameter sections introduces points with significantly lower bending stiffness compared to the thicker upper sections. Moreover, the multiple joints required for extension add potential compliance. These thinner lower segments and their associated locking mechanisms often become the primary bottleneck in overall system rigidity, acting as pivot points that amplify movement induced by forces applied higher up the structure.
Achieving Sharp Vertical Shots on a Tripod - Choosing the Vertical Camera Mount Method
When addressing how to orient your camera vertically on the tripod, you essentially have a few core approaches, each with implications for stability. The most common way, if your equipment allows, is to use the built-in tilt function of your tripod head, turning the camera assembly 90 degrees so it hangs to the side of the head's central axis. This is quick, assuming your head has that range of motion. However, a more robust method involves an L-bracket, a piece of metal that bolts onto the base and side of your camera body. This bracket provides a second mounting surface on the 'bottom' when the camera is turned vertically. By attaching the camera via the L-bracket to the tripod head, the camera's weight stays much closer to being centered directly above the head's mechanisms and the tripod legs. This approach offers significant stability advantages over side-tilting the head, and also allows you to flip quickly between horizontal and vertical framing simply by unclamping and reclamping the camera on the bracket's alternative side without needing to drastically alter the head's position. While less common for typical vertical shots, specialized arms or alternative mounting plates might be used in unique situations to position the camera, but these often come with their own challenges in maintaining absolute rigidity. Choosing the right physical interface between your camera and the tripod head is a critical first step towards a sharp vertical shot.
Here are some points regarding the technical implications of selecting the mounting strategy for vertical camera orientation:
Tilting the camera vertically using a standard ball head setup positions the camera body such that its longest dimension is often presented as a large, relatively flat surface orthogonal to typical horizontal airflow. This geometry fundamentally increases the effective cross-sectional area encountering the wind, leading to substantially higher aerodynamic drag forces compared to an L-bracket setup where the camera body's long axis is oriented horizontally relative to potential wind direction. This amplified drag introduces a greater dynamic load source, increasing susceptibility to wind-induced vibration.
When a camera on a standard plate is tilted 90 degrees within a ball head's clamp, the gravitational load vector shifts from being largely axial (along the ball's center) to exhibiting a significant tangential component. This imparts considerable shear stress onto the ball's locking mechanism, forcing it to resist the load primarily through frictional grip on the angled surface. This mechanical loading is less favorable than the predominantly compressive forces typically handled by the ball head's locking mechanism when the camera is mounted horizontally or vertically via an L-bracket where the load is transmitted more directly downwards onto the head's base.
Achieving precise fine-tuning of composition when tilting a ball head vertically typically requires minute adjustments to the ball's locked position, potentially involving simultaneous manipulation across different planes. In contrast, utilizing an L-bracket allows the camera to be mounted upright, retaining full, independent control over the tripod head's horizontal panning axis. This permits precise side-to-side framing adjustments using the head's dedicated pan base, which is often engineered for smoother and more repeatable micro-movements than repositioning a locked, heavily loaded ball.
The mechanical pathway for vibration transmission and dissipation differs between methods. An L-bracket establishes a more direct, structurally continuous connection between the camera's chassis and the tripod head's main mounting surface. This provides a potentially more efficient route for camera-generated vibrations (e.g., shutter shock) to propagate into the larger, more damping mass of the head and tripod legs. Routing these forces through the stressed and angled surfaces of a tilted ball joint might introduce compliance or less efficient energy transfer pathways, potentially allowing vibrations to persist longer within the camera/head interface.
The critical interface where the camera attaches to the quick-release plate is subjected to fundamentally different stress profiles depending on the mounting method. When a camera is tilted vertically on a ball head using a standard plate, the camera's weight creates substantial rotational torque around the mounting screw axis due to the cantilevered mass. This can test the rigidity and grip of the camera-to-plate connection, potentially leading to minute rotational play. An L-bracket, by shifting the mounting point closer to the camera's center of gravity, loads this interface primarily in compression and shear perpendicular to the screw axis, a configuration offering inherently greater resistance to rotational movement and flex at this vital connection.
Achieving Sharp Vertical Shots on a Tripod - Addressing Ground and Environmental Stability
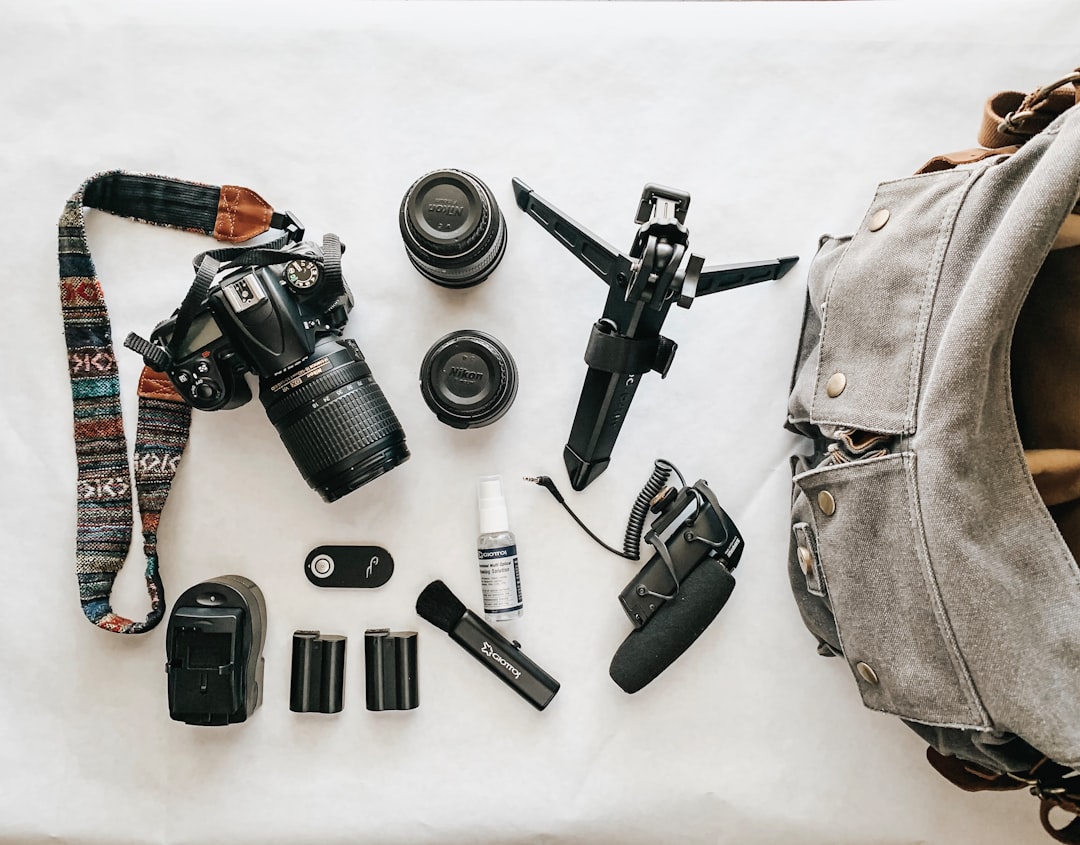
Achieving critically sharp vertical images while using a tripod relies heavily on ensuring the foundation you place it on and the surrounding conditions are as stable as possible. The ground itself acts as the initial base for the entire setup; its nature profoundly impacts how still the camera can remain. Standing on firm, unyielding terrain offers a stark contrast in stability compared to soft sand, loose soil, or uneven, rocky patches, all of which can introduce unwelcome movement or vibrations into the system. This inherent ground instability can easily propagate up the tripod legs, undermining even the sturdiest gear and causing image-degrading blur. Beyond the immediate footing, environmental factors like wind applying pressure against the camera's side or even subtle shifts in the earth can further compromise stability. Addressing these external elements by seeking out the most stable possible patch of ground and shielding the setup from wind is a foundational requirement for success before fine-tuning composition or exposure settings for those tall shots. Ignoring the ground means building on a potentially shaky platform from the start.
The subtle transmission paths of ambient kinetic energy through seemingly rigid substrates pose a challenge. Even 'solid' ground transmits minute vibrations, and a vertically cantilevered mass atop a tripod can act as a sensitive accelerometer, amplifying displacements near its resonant frequencies, which are distinct from the system's horizontal modes and often more easily excited by vertical forces.
The heterogeneous and often elastic nature of underlying soil or substrate can lead to time-dependent mechanical creep under the concentrated point loads applied by tripod feet, particularly with asymmetric vertical loading. This subtle, differential settlement introduces a slow, unpredictable drift in the vertical alignment, undermining critical sharpness requirements over time.
Differential thermal expansion coefficients across tripod materials, exacerbated by uneven environmental heating (e.g., direct solar radiation on one leg), induce internal stresses and dimensional changes. Over extended observation periods required for techniques like exposure bracketing or stacking, these minute structural deformations can disrupt the precise positional consistency.
Beyond bulk drag, a camera assembly positioned vertically presents bluff body characteristics, potentially inducing oscillating pressure fields via mechanisms like von Kármán vortex streets in even modest airflow. These periodic forces, if near the system's resonant frequencies, represent a dynamic excitation source distinct from constant wind pressure and difficult to passively mitigate effectively across all wind conditions.
The efficacy of vibration isolation or damping is fundamentally governed by the impedance match and mechanical coupling at the tripod foot-to-ground interface. The choice of foot material, shape, and contact pressure dictates the transmission efficiency of environmental noise into the tripod and the dissipation rate of system-generated oscillations into the ground, a critical, often overlooked boundary condition in overall system stability analysis.
More Posts from colorizethis.io: