Precision Colorization for Optimal Weld Detail
Precision Colorization for Optimal Weld Detail - Decoding Microstructural Information Through Color Algorithms
While the foundational concept of decoding microstructural information through color algorithms has been around, recent years leading into mid-2025 have seen notable shifts in its application and underlying challenges. The drive for increasingly automated analysis has pushed the sophistication of these algorithms, moving beyond simple visual aids towards attempts to directly infer critical material properties from subtle color gradients and patterns. This accelerated approach aims to expedite defect identification and quality assurance in complex materials, yet it places an even greater demand on the algorithms' interpretation accuracy to avoid mischaracterizing vital structural features. A persistent discussion revolves around the transferability of these color-encoded insights across varying material chemistries and fabrication methods, prompting questions about whether the efficiency gained truly translates to a deeper, more reliable metallurgical understanding. The ongoing task is to ensure these algorithmic interpretations genuinely augment, rather than potentially oversimplify, the nuanced complexities of microstructural data.
We've been keenly observing what "Decoding Microstructural Information Through Color Algorithms" reveals:
* It's quite remarkable how many distinct chromatic variations these computational approaches can resolve, far beyond what the human eye typically perceives as unique hues. Each subtle color shift we encounter often corresponds to a specific crystallographic orientation or a variation in phase distribution, allowing for an incredibly precise mapping of microscopic boundaries and compositions. This granularity of information is a significant leap.
* The true power, as we're discovering, lies in transforming these visual cues into precise quantitative metrics, moving decisively beyond qualitative assessment. Instead of merely subjective visual inspection, these algorithms yield hard numbers for things like average grain size, aspect ratios, or even the volumetric fraction of different intermetallic compounds. This numerical output is absolutely critical for rigorous quality control and for accurately predicting how materials will perform.
* What's particularly fascinating is how these unique chromatic signatures illuminate microstructural features that are either completely invisible or incredibly challenging to discern using traditional black-and-white microscopy. We've seen them uncover specific types of grain boundaries or even very subtle precipitates that were previously overlooked. It truly feels like peeling back a layer to reveal hidden information within the material's structure.
* A promising avenue, still under active exploration, is the potential for these algorithms to serve as a non-destructive predictor for mechanical performance. If we can reliably link distinct color patterns to previously characterized material properties, such as tensile strength, ductility, or fatigue life, it could revolutionize rapid quality assessment. Imagine quickly analyzing a weld's microscopic appearance to estimate its performance without needing to stress-test it.
* Traditional metallographic analysis has long grappled with subjectivity, heavily relying on individual human interpretation of etched samples, which is prone to variability and limited by visual acuity. Color algorithms fundamentally address this, ushering in an era of objective, highly repeatable analysis. They can process vast datasets with an unparalleled level of consistency and speed, overcoming significant historical limitations in material characterization.
Precision Colorization for Optimal Weld Detail - Enhancing Anomaly Detection in Weld Seams
The current emphasis on enhancing anomaly detection specifically within weld seams signifies a distinct progression for precision colorization methodologies. While the underlying principles of deriving material insights from intricate color patterns have seen considerable development, their application to the uniquely complex and often heterogeneous microstructures found in weld zones presents novel challenges and opportunities. This targeted evolution moves beyond general defect identification to explore the specific morphological and compositional signatures of anomalies inherent to welding processes, such as subtle types of porosity, fine-scale cracking, or detrimental phase segregations. The ongoing effort centers on developing algorithms capable of reliably distinguishing and characterizing these specific weld imperfections amidst the varied thermal and mechanical histories within a weld, acknowledging the inherent variability across different welding techniques and material combinations. This specialized focus seeks to offer a more nuanced understanding of weld integrity, potentially informing not only initial quality checks but also predictive models for component longevity.
It's quite intriguing how current color algorithms are starting to truly differentiate specific flaw types – not just "there's a defect," but "that's likely an oxide inclusion, not a micro-fissure." This nuanced distinction, often leveraging spectral data beyond simple visible light, allows for a far more granular understanding of what's *actually* happening within the weld, even within notoriously complex or novel material compositions. However, the reliability of this distinction under high variability of real-world impurities still warrants rigorous cross-validation.
We're seeing deep learning frameworks, honed on expansive collections of these enriched images, demonstrate an impressive ability to concurrently pinpoint and categorize various anomalies. While their speed far outstrips manual inspection, the claim of "rivaling human experts" often requires careful qualification; human insight remains crucial for ambiguous cases or unforeseen defect morphologies, but for repetitive, high-volume tasks, their consistency is undeniable.
A particularly exciting development is the algorithms' evolving capacity to flag what appear to be the very first signs of material distress – faint chromatic shifts that could precede macroscopic issues. This moves us from merely spotting a flaw once it's established to potentially catching its precursors, prompting an intriguing shift toward truly preemptive material assessment, rather than just reactive quality checks after a problem has solidified.
A major hurdle we’ve wrestled with, the "transferability" across diverse materials, is beginning to see some encouraging breakthroughs. Certain advanced algorithms are indeed showing a remarkable ability to self-tune their representation parameters, adapting to highlight anomalies in unfamiliar or highly engineered weld compositions without demanding an entirely new, time-consuming re-calibration for every unique alloy. While "without extensive re-calibration" might be a strong claim for truly *exotic* new materials, it certainly simplifies deployment in many common variations.
What's also emerging is how this precision colorization effort is now reaching beyond the confines of standard visible light, incorporating data from multispectral and even hyperspectral sources. This allows us to construct complex "false-color" representations that are essentially translating an array of invisible spectral information into visual cues, uncovering subtle chemical variations or crystallographic irregularities within the weld that traditional optical inspection simply misses altogether. The challenge, of course, is interpreting the sheer volume of this multi-dimensional data effectively.
Precision Colorization for Optimal Weld Detail - Navigating Calibration and Data Integrity Challenges
The discourse surrounding calibration and data integrity in precision colorization for weld analysis has significantly deepened as of mid-2025. We're now contending with the intricacies of self-calibrating systems, where algorithmic biases or subtle drifts in sensor arrays can cascade into profound inaccuracies, challenging our traditional notions of control. The sheer scale of data generated by advanced multi-spectral imaging in industrial settings has likewise elevated concerns; ensuring end-to-end data provenance and guarding against subtle corruption or loss during high-volume processing presents a persistent, complex hurdle. Furthermore, as these systems move towards real-time, in-line application, the very definition of data 'integrity' must evolve to encompass dynamic validation and adaptive correction mechanisms, far beyond static verification checks. This ongoing evolution demands a continuous re-evaluation of trust in automated insights.
Even in environments meticulously controlled for environmental stability, we're finding that minute temperature shifts, as small as a mere five-hundredths of a degree Celsius, can subtly but significantly influence the baseline responses of hyperspectral sensors. This necessitates the development of remarkably advanced compensation algorithms to prevent us from misinterpreting a sensor's transient drift as an actual change in the material's microstructure, a subtle yet persistent issue in achieving truly reliable raw data.
Interestingly, our current precision colorization systems are progressively moving away from a sole reliance on periodic, human-driven calibration cycles. Instead, we're seeing an increasing deployment of AI-driven diagnostic routines that continuously monitor sensor output. These systems proactively flag nascent calibration deviations by comparing real-time chromatic data against established historical performance baselines, aiming to catch subtle inaccuracies before they propagate into larger interpretational errors.
A growing concern in data integrity now revolves around differentiating genuinely acquired microstructural imagery from increasingly sophisticated synthetically generated or even maliciously altered datasets. If compromised data is inadvertently used for algorithm training, it could lead to critically flawed characterizations of weld anomalies. Consequently, the development of novel statistical "fingerprinting" techniques to detect these subtle manipulations is becoming an essential research area.
A particularly formidable calibration hurdle continues to be the accurate colorimetric interpretation for rare or previously undocumented microstructures, sometimes colloquially referred to as "dark data." Generating sufficient, reliable ground-truth samples for these highly specific or anomalous edge cases proves prohibitively difficult and time-consuming. This challenge significantly drives our current efforts toward developing physics-informed models that can extrapolate beyond limited empirical training data, providing more robust interpretations.
To achieve truly dependable metrological traceability for color-based microstructural analysis, a promising direction involves the creation and validation of high-fidelity "digital twins" for our physical calibration standards. These virtual counterparts offer the intriguing possibility of on-demand calibration validation and performance audits, circumventing the inherent wear and tear, and potential degradation, associated with repeated use of delicate physical reference materials.
Precision Colorization for Optimal Weld Detail - Current Trajectories for Automated Weld Inspection
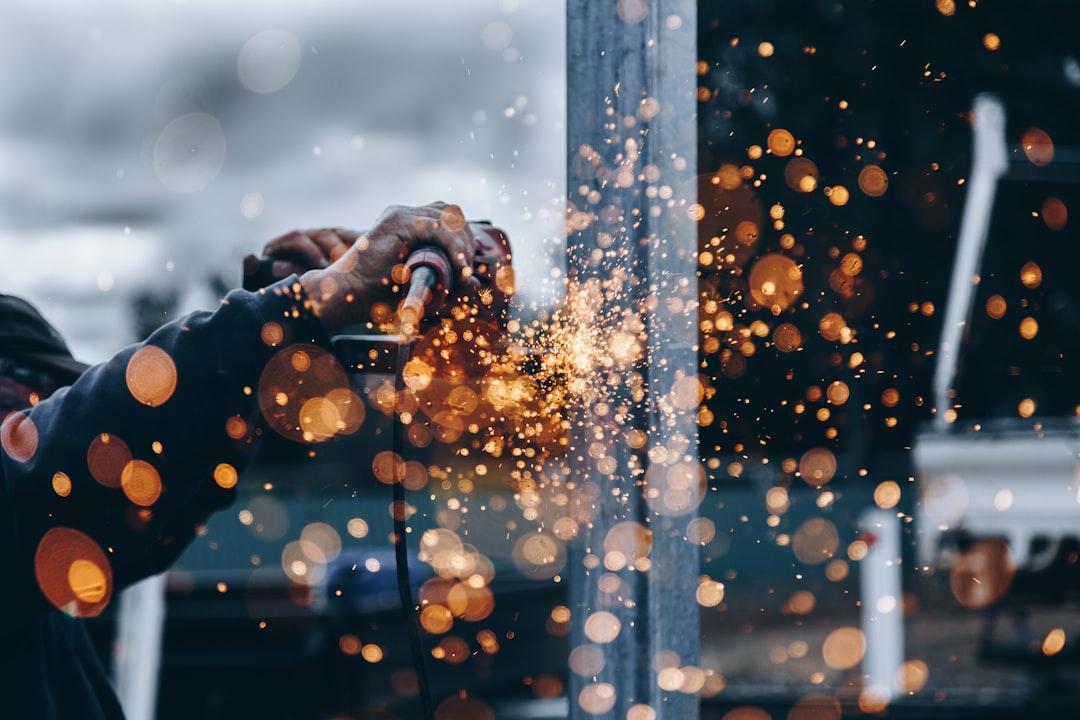
As of mid-2025, the focus in automated weld inspection is increasingly shifting from mere anomaly identification to a more profound integration of analytical capabilities directly into manufacturing pathways. The evolving trajectory isn't just about detecting flaws; it's about harnessing detailed data, including the subtle insights from chromatic analysis, to dynamically monitor weld integrity and inform real-time adjustments throughout the fabrication process. This shift heralds a potential move beyond traditional post-production quality checks towards continuous, predictive assessment. However, this advanced integration necessitates highly robust validation mechanisms and a critical understanding of how these complex systems perform under variable industrial conditions, especially as their application scales, raising new questions about oversight and potential unintended consequences of over-reliance on automated interpretations.
It’s becoming clear that current automated inspection setups are no longer merely diagnostic; they are actively influencing the very act of welding. We're observing systems capable of feeding instantaneous microstructural observations directly back to the welding apparatus, facilitating autonomous, minor corrections to parameters like heat input or material deposition rate mid-process. This closed-loop approach means the weld can, in theory, 'self-correct' to preemptively reduce the likelihood of flaws during its formation, which is a significant departure from post-process detection. The challenge, of course, lies in the latency and reliability of these real-time microstructural interpretations under dynamic conditions.
We are also seeing efforts push beyond simple two-dimensional surface or cross-sectional views. A promising, albeit labor-intensive, trajectory involves integrating sequential material removal techniques (like focused ion beam milling or precision grinding) with colorimetric imaging to construct genuine, high-resolution three-dimensional digital models of the weld’s internal architecture. This volumetric mapping allows us to truly visualize and quantify the complex spatial arrangement of features such as intricate networks of internal voids or the nuanced, interwoven distribution of different phases, offering a deeper insight that traditional planar analysis often misses.
Perhaps one of the most intriguing developments is the aspiration to non-destructively infer the internal stress state within weld regions. There’s ongoing research to correlate subtle color variations with underlying crystallographic textures and dislocation patterns, which are inherently tied to residual stresses. If this correlation proves robust and generalizable, it could offer a novel, rapid pathway to estimate internal stresses – a crucial factor for predicting how components will behave under long-term cyclic loading and a key determinant of eventual fatigue performance, without resorting to more complex, time-consuming techniques. However, translating color patterns directly to a complex tensor field of stress remains a formidable hurdle.
We’re moving beyond systems that simply match observed patterns to a pre-existing catalog of known flaws. Some of the latest algorithmic developments are employing unsupervised learning approaches, allowing them to autonomously pinpoint statistically unusual color configurations. This means the system can, theoretically, flag entirely novel or previously undocumented microstructural anomalies that don't fit any predefined categories, potentially accelerating our recognition of truly unforeseen failure pathways. This shift is particularly exciting for new materials or processes where exhaustive defect libraries simply don't exist, though validating these "unclassified" findings often requires extensive follow-up.
The detailed color-encoded microstructural data generated by these automated inspection systems is beginning to find its way into the larger digital twin ecosystems being developed for manufactured parts. This allows for a component's virtual counterpart to be continuously updated with real-time, microscopic insights into its internal condition. The vision here is to enable more sophisticated, dynamic predictive maintenance strategies and potentially extend the effective operational life of assets by monitoring subtle changes in their internal weld structures, rather than relying solely on macroscopic degradation models. The true test, however, will be the reliability of linking micro-scale changes to macro-scale component performance in real-world scenarios.
More Posts from colorizethis.io: